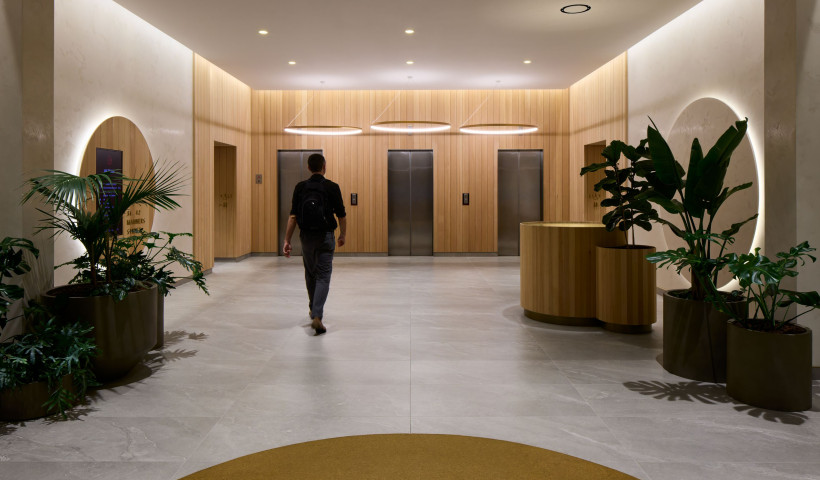
In designing, two key considerations to be taken into account for multi-level specification are acoustics and flammability. With over 100 years combined experience in commercial projects, the Tile Warehouse team has the ability to advise and assist you on product specification, installation and fit-for-purpose solutions.
Acoustics
The Tile Warehouse specification team recommend acoustic systems from either Ardex or Construction Chemicals, depending upon project requirements.
Construction Chemicals Approved system: Acoustibond/Acoustifloor
‘Liveability’, in noise attenuation, is the one single quality that all owners and tenants desire in multi-level dwellings. This is achievable by the use of suitable acoustic flooring systems over tile.
Construction Chemicals' acoustic flooring compound has been applied to many apartments, commercial buildings, retirement villages and high-end residential homes throughout New Zealand and Australia, including Sky City Casino.
Two proven acoustic systems are Construction Chemicals' Acoustiflor and Acoustibond, which can be used independently or together, depending on required results. For maximum performance, the Tile Warehouse team recommends Acoustibond on top of Acoustiflor.
Acoustibond is a rubberised tile adhesive, which is spread using a 15mm notched trowel. Once tiles are embedded into Acoustibond, it forms a 4mm rubber matt. This system saves even more time, as the tiler can lay the acoustic system and tiles at the same time.
Acoustiflor is poured like a floor levelling compound which can be laid much quicker than mat systems, saving so much time in labour. It won't dis-bond like mat systems, causing a drummy sound, due to the adhesive being in the product itself. Acoustiflor also has levelling properties, which takes up some undulations/voids in the substrate too.
‘Deformability’ is common problem experienced by those installing over less than flat surfaces. The combination of Acoustibond/Acoustiflor was installed across 14,000m² at the Auckland Airport for this exact purpose to eliminate cracking of grout and adhesion issues.
Neither the creativity of the external design of a building nor the niceties used in the fit-out matter much to a resident who finds their every-day living is compromised by annoying noise from adjoining apartments, either from above or next door. Bearing this in mind, it is somewhat disconcerting to see so many buildings designed or constructed with the lowest common denominator for sound transmission between floors in higher density accommodation. The Building Code regulates minimum acceptable construction standards with many members of the construction industry interpreting them as absolute requirements. However, the remedy to this is a cost-effective fix that adds thousands to the value of the dwelling and can be marketed as a 4 or 5 Star building.
A well-designed floor ceiling combination that meets the Building Code minimum sound attenuation requirement is 62 LnTw. Most builders accept this, however, a 4 or 5 Star liveability indexed building can be attained if more attention is given to accentuated add-on product. For example, a floor tested at 60 LnTw fits the 2 Star category, but by the simple addition of Acoustibond Acoustic Adhesive prior to laying the floor tiles, means a full 4mm bed of acoustic membrane beneath resulting in a 48 LnTw reading. This is a full 12 decibels below the bare slab reading, achieving a 4 Star rating. Applying the Acoustiflor acoustic membrane first results in a 5 Star.
Construction Chemicals manufactures every component of their acoustic system meaning compatible acrylic polymer-modified technology from top to bottom, unlike the commonly used mats based on polyurethane binders which significantly reduce adhesion both above and below the mats.
NB: These mats are not manufactured by the company supplying them, and repel cement-based adhesives, hence why there are so many failures after six to twelve months of application.
Ardex approved system:
DS70
ARDEX is able to supply a full soundproofing system for impact insulation to meet IIC requirements all the way from sub-floor preparation, soundproof matting, tiling systems through to the finished grout and silicones. Having one supplier for the whole system ensures that the architects only have one point of contact to work with and have the peace of mind that comes from using a single tested and warrantied system. Combine that with their recommended first-grade quality tile and stone-composite flooring from Tile Warehouse ensures a full system warranty. Architects today are looking for such security from the ground floor.
Benefits of the ARDEX DS70 System:
- Sound reduction for tile, stone or wood floor coverings
- Crack isolation protection (up to 3 mm)
- Set tile and stone directly onto ARDEX DS 70 with a variety of ARDEX adhesives
- Environmentally friendly; made from 92% recycled rubber
- Fast and easy installation using ARDEX AF180 pre-mixed adhesive
- ARDEX DS 70 Systems achieve Light Commercial through Extra Heavy Commercial ratings (per ASTM 627 Robinson Test)
- Independently tested in NZ for its acoustic rating by Auckland Uniservices Limited (University of Auckland)
- Onsite field test results show remarkable performance against other 'like' systems
- BRANZ appraised waterproofing system
Avoiding that common issue, 'Deformability':
The Robinson test is used to determine deformability. "This test method covers the evaluation of complete floor tile installation systems...for failure under loads.”
Contact the Tile Warehouse commercial team to discuss the above system's suitability for your next multi-dwelling project.
Flammability
In NZ, fire ratings are specified in our Building Code to ensure that if a building is on fire, construction materials do not significantly increase the spread or intensity of a fire. Tiles, being inert and non-combustible, do not require testing as they do not contribute to fire. By nature also, tiles do not contain any form of petroleum-based product or wood fibres and therefore in essence, are fireproof and non-toxic.
For this reason, any petroleum-based, flammable hard finishes such as flooring would be of concern to those in medium density housing.
Being fired at very high temperatures means ceramic tiles do not exude VOC emissions. During manufacture, any organics that might be present in clays or binders are completely burned away. As a result, the final product is inert, and no VOCs can be emitted. Aside from this, quality porcelain tiles contain no sealants, waxes or other chemicals that could release VOCs into the environment.
View further specification details in Tile Warehouse's Fire Performance Brochure