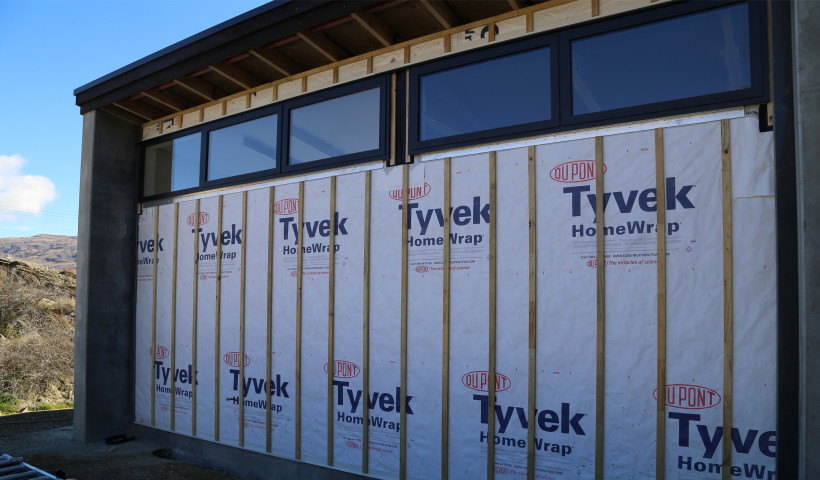
Flashing tapes are designed to create a reliable joint that helps seal the interface between wall penetrations and wall system components such as windows and doors. Flashing tapes also help divert incidental water back out towards the exterior. As they are a crucial component in helping prevent water from damaging walls, it is important to specify flashings that will perform under the various conditions that a wall system may be exposed to.
Today, the most popular are self adhered 'peel and stick' tapes that create a tighter, more continuous seal than metal or non-adhesive flashings. These consist of a top sheet, an adhesive seal typically made from rubber, modified asphalt (bitumen) or butyl rubber components, and a release liner.
The release liner is peeled off to expose the adhesive that holds the flashing in place and seals the joint. The top sheets strengthen the flashing to guard against handling damage during installation, serve as a water-resistant layer and help prevent UV Rays in sunlight from degrading the adhesive. Most top sheets are plastic films or foils, although some are stretchable laminates such as DuPont FlexWrap.
What determines Flashing Performance?
There are many factors that impact the performance of self adhered flashing products. In addition to forming a reliable, durable seal to the substrate, other performance attributes include:
- Ease of installation
- Range of installation conditions
- Physical property attributes of the flashing
Weather resistance, thermal resistance and adhesion durability are the most important properties to look for.
DuPont Testing
In testing performed by DuPont that simulated conditions typically encountered during and after construction that can cause flashings to fail, performance and durability differences in the top sheets and adhesives used in commercially available flashings were discovered.
Accelerated weathering with UV light, heat and moisture degraded flashings with asphalt adhesives significantly more than those with butyl adhesives. The asphalt based flashing showed significant curling and delaminating from the sheathing surface. Top sheet degradation and adhesive embrittlement were also observed.
Tests of thermal and moisture resistance revealed differences in adhesive and top sheet durability. Although the building’s exterior siding can protect flashing from UV light degradation after installation, it is still vulnerable to long-term thermal exposure within the wall. It is essential that the top sheet be made of a highly durable material so that it provides integrity to the flashing and helps maintain a continuous seal between the window and wall.
Key differences were also noted in moisture performance. Asphalt based flashing tapes exhibited almost total loss of adhesion to OSB sheathing when immersed in water for one week, while the DuPont flashings maintained over 85% of their peel strength.
To conclude, DuPont butyl flashings outperformed commonly used asphalt based flashing products, even after exposure to thermal ageing and showed superior dimensional stability and resistance to adhesive flow.
It is noted that when applying all flashing tapes to LOSP treated timber, allow a minimum of 1 week for the solvents in the LOSP treatment to evaporate.
About DuPont Flashing Tapes
- DuPont FlexWrap and DuPont Flashing Tape are CodeMark certified and can be installed when the temperature of the flashing adhesive is above -4C.
- DuPont Flashing tapes contain no asphalt and use a 100% butyl based adhesive.
- DuPont Flashing tapes can be exposed to UV light for up to 120 days during construction.
- DuPont Flashing tapes, when installed in sill corners, do not need plastic corners or adhesive primer when the temperature of the flashing tape is above -4C.
- DuPont Flashing tapes can achieve a risk score of between 0-20 in accordance with NZBC Acceptable Solution E2/AS1, Table 2 and can be installed in Building Wind Zones up to and including very high per NZS3604:1999.