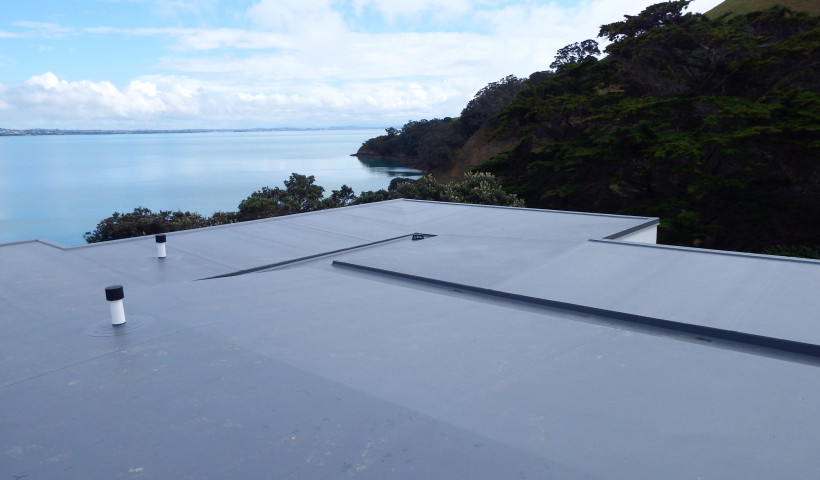
A conventional roof assembly would typically consist of a structural deck with an insulation layer placed either below or above, followed by the roof membrane. This membrane could be fully adhered, mechanically attached, or ballasted to hold it in place. In a hot rubberised asphalt PMR assembly, the roof membrane is fully bonded to the structural deck, followed by XPS insulation then ballast. Basically, placement of the roof membrane and insulation layer in a PMR assembly is reversed or inverted.
In many cases slope in the roof deck structure may not be practical because of its size, shape, materials available and cost, considering that it is typically more expensive to provide a sloped roof structure than a perfectly flat one. Therefore, the industry turns to various methods of adding slope to structurally flat roof decks. The resulting effort to provide slope is often in conflict with practical considerations and in the end, results in the owner getting a roof with serious built-in problems.
Two of the more common methods used to provide slope on flat concrete structural decks are by pouring on top of the deck a concrete sloped topping slab, adding a layer of screed, or by placing tapered insulation boards, specifically fabricated to fit the roof's configuration. The use of this secondary substrate to create slope can lead to numerous problems.
The secondary substrate can trap moisture between the structural deck and the roof membrane during construction. This moisture present within the assembly can lead to membrane blistering and separation from the substrate (if adhered) and perhaps long-term deterioration.
If the roof membrane were to leak for any reason, the leakage would not be readily traceable because water would be free to move laterally throughout the void (between the membrane and the structural deck), before finding its way to a crack or opening in the deck where it could enter the building. To trace and repair such a leak would be a nightmare and could result in the removal of much of the build-up covering the membrane in pursuit of the leak’s location.
The above stated built-in problems are much more serious than lack of slope to drains in the function of a PMR assembly. With a PMR assembly on a zero fall/flat structural deck, upwards of 60% of the water flows over the XPS insulation layer to the drains, thereby creating a raised drainage level plane or “plateau drainage”, elevated well above the drains at the membrane level, thereby accomplishing all the functions of positive slope. The balance of the water in the joints between the boards flows freely to a drain, and any that finds its way beneath the boards is displaced by the boards and the ballast weight above.
Zero-Pitch Roofs Drain
Typical PMR zero-pitch roofs drain quite well because of the PMR design itself. A simple analogy can be used to illustrate this. Pour water on a flat surface and watch what happens. It moves to the easiest escape route. In the case of a table, the water will flow or be pushed towards the edge. On a roof, the water pushes toward the drains. Taking the analogy further, place a solid weight on the liquid that is left on the table. The remaining water is displaced to the edge of the table, or in the case of a roof, the drains. Essentially, that is how PMRs are designed. In service, the ballasted in place insulation in most cases does not allow water to build up in the first place. The space where water may accumulate is taken up by the insulation. As a result, the water that does not flow off the surface of the insulation is immediately displaced to the provided outlets. Furthermore, unlike conventional roofs which once wet, stay wet and deteriorate, PMR applications can dry out as they are designed as open systems.
Rubberised asphalt was conceived initially as a waterproofing membrane to be subjected to long term submersion. Fully protected, as it typically is in a PMR assembly, water may sit in direct contact with the membrane indefinitely with no adverse effect on the material’s integrity.
“Positive slope to drain” works best if it can be accomplished in the original structure and not by the installation of a secondary substrate to provide the desired slope. “Raised plateau drainage” is an old concept that provides the benefits of slope, simplified construction, is cost-effective and has a long successful track record.
Written by Chris Ross, Allco